Projektowanie i budowa maszyn przemysłowych to proces, który wymaga staranności oraz przemyślanej strategii. Kluczowe etapy tego procesu zaczynają się od analizy potrzeb klienta oraz specyfikacji technicznych, które określają, jakie funkcje maszyna ma spełniać. Na tym etapie inżynierowie muszą zrozumieć wymagania dotyczące wydajności, bezpieczeństwa oraz ergonomii. Kolejnym krokiem jest koncepcja maszyny, która obejmuje tworzenie wstępnych rysunków i modeli 3D. Wykorzystuje się do tego nowoczesne oprogramowanie CAD, które pozwala na wizualizację projektu oraz identyfikację potencjalnych problemów jeszcze przed rozpoczęciem produkcji. Po zatwierdzeniu koncepcji następuje faza prototypowania, gdzie powstaje pierwszy model maszyny. Prototyp jest testowany pod kątem wydajności oraz zgodności z wymaganiami klienta. Na podstawie wyników testów wprowadza się niezbędne poprawki, co prowadzi do finalizacji projektu i rozpoczęcia produkcji seryjnej.
Jakie technologie są wykorzystywane w budowie maszyn przemysłowych
W dzisiejszych czasach projektowanie i budowa maszyn przemysłowych opierają się na zaawansowanych technologiach, które znacznie zwiększają efektywność oraz precyzję produkcji. Wykorzystanie technologii CNC, czyli komputerowego sterowania numerycznego, pozwala na automatyzację procesów obróbczych, co przekłada się na wyższą jakość wykonania elementów maszyn. Dodatkowo, druk 3D staje się coraz bardziej popularny w produkcji prototypów oraz części zamiennych, umożliwiając szybkie wytwarzanie skomplikowanych kształtów bez potrzeby stosowania tradycyjnych metod obróbczych. W zakresie materiałów inżynieryjnych stosuje się kompozyty oraz stopy metali o wysokiej wytrzymałości, co pozwala na redukcję masy maszyny przy jednoczesnym zachowaniu jej trwałości. Technologie automatyzacji i robotyzacji również odgrywają kluczową rolę w budowie nowoczesnych maszyn przemysłowych, umożliwiając zwiększenie wydajności linii produkcyjnych oraz minimalizację błędów ludzkich.
Jakie są najważniejsze aspekty bezpieczeństwa w projektowaniu maszyn
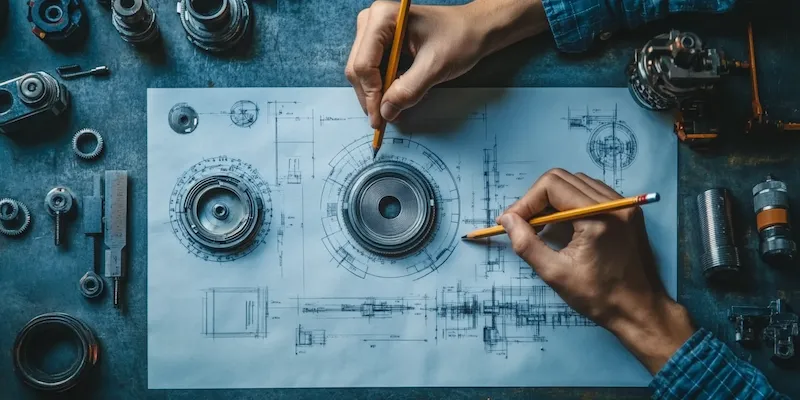
Projektowanie i budowa maszyn przemysłowych
Bezpieczeństwo jest jednym z najważniejszych aspektów, które należy uwzględnić podczas projektowania i budowy maszyn przemysłowych. Przepisy dotyczące bezpieczeństwa pracy nakładają obowiązek zapewnienia odpowiednich zabezpieczeń dla operatorów oraz osób znajdujących się w pobliżu maszyny. W tym celu inżynierowie muszą przeprowadzać analizy ryzyka związane z użytkowaniem maszyny, identyfikując potencjalne zagrożenia i opracowując strategie ich eliminacji lub minimalizacji. W projektach uwzględnia się różnorodne rozwiązania ochronne, takie jak osłony mechaniczne, systemy awaryjnego zatrzymania czy czujniki obecności operatora. Ważnym elementem jest także ergonomia stanowiska pracy, która wpływa na komfort użytkownika oraz zmniejsza ryzyko urazów związanych z długotrwałym użytkowaniem maszyny. Szkolenie pracowników w zakresie obsługi maszyn oraz procedur bezpieczeństwa jest równie istotne, aby zapewnić prawidłowe i bezpieczne korzystanie z urządzeń.
Jakie są trendy w projektowaniu nowoczesnych maszyn przemysłowych
W ostatnich latach projektowanie i budowa maszyn przemysłowych uległy znacznym zmianom pod wpływem postępu technologicznego oraz rosnących oczekiwań rynku. Jednym z najważniejszych trendów jest automatyzacja procesów produkcyjnych, która pozwala na zwiększenie wydajności oraz redukcję kosztów operacyjnych. Wprowadzenie robotyzacji do linii produkcyjnych umożliwia realizację skomplikowanych zadań z dużą precyzją i powtarzalnością. Kolejnym istotnym kierunkiem rozwoju jest integracja systemów IoT (Internet of Things), które pozwalają na zbieranie danych w czasie rzeczywistym oraz ich analizę w celu optymalizacji procesów produkcyjnych. Maszyny stają się coraz bardziej inteligentne dzięki zastosowaniu sztucznej inteligencji i uczenia maszynowego, co pozwala na samodzielne podejmowanie decyzji dotyczących np. konserwacji czy dostosowywania parametrów pracy do zmieniających się warunków. Zrównoważony rozwój również ma duże znaczenie w projektowaniu nowoczesnych maszyn; producenci starają się ograniczać zużycie energii oraz emisję szkodliwych substancji poprzez wdrażanie ekologicznych rozwiązań technologicznych.
Jakie są kluczowe czynniki wpływające na koszt budowy maszyn przemysłowych
Koszt budowy maszyn przemysłowych jest złożonym zagadnieniem, które zależy od wielu czynników. Przede wszystkim, materiały używane do produkcji mają ogromny wpływ na ostateczny koszt. Wybór wysokiej jakości komponentów, takich jak stal nierdzewna czy zaawansowane tworzywa sztuczne, może znacząco podnieść cenę maszyny, ale jednocześnie zwiększa jej trwałość i wydajność. Kolejnym istotnym aspektem jest skomplikowanie projektu; im bardziej złożona maszyna, tym więcej czasu i zasobów wymaga jej budowa. Koszty pracy również odgrywają kluczową rolę; w krajach o wyższych stawkach płac całkowity koszt produkcji będzie wyższy. Dodatkowo, procesy takie jak prototypowanie oraz testowanie maszyny mogą generować dodatkowe wydatki, które należy uwzględnić w budżecie. Warto również zwrócić uwagę na koszty związane z certyfikacją i spełnianiem norm bezpieczeństwa, które są niezbędne do wprowadzenia maszyny na rynek.
Jakie umiejętności są potrzebne w projektowaniu maszyn przemysłowych
Projektowanie i budowa maszyn przemysłowych wymagają szerokiego wachlarza umiejętności oraz wiedzy technicznej. Inżynierowie zajmujący się tym obszarem muszą posiadać solidne podstawy w dziedzinie mechaniki, elektroniki oraz automatyki. Znajomość zasad działania różnych systemów mechanicznych oraz elektronicznych jest kluczowa dla skutecznego projektowania maszyn. Umiejętności analityczne są równie ważne; inżynierowie muszą być w stanie przeprowadzać analizy ryzyka oraz oceniać wydajność projektowanych rozwiązań. Dodatkowo, biegłość w obsłudze programów CAD oraz CAM jest niezbędna do tworzenia precyzyjnych modeli 3D oraz planów produkcyjnych. Komunikacja interpersonalna również odgrywa istotną rolę, ponieważ inżynierowie często współpracują z innymi specjalistami, takimi jak technicy czy menedżerowie projektów. Umiejętność pracy w zespole oraz zdolność do rozwiązywania problemów są kluczowe w dynamicznym środowisku produkcyjnym.
Jakie są najczęstsze problemy napotykane podczas budowy maszyn przemysłowych
Budowa maszyn przemysłowych to skomplikowany proces, który może wiązać się z wieloma problemami i wyzwaniami. Jednym z najczęstszych problemów jest niedostateczna komunikacja między członkami zespołu projektowego. Brak jasnych informacji dotyczących wymagań klienta lub specyfikacji technicznych może prowadzić do poważnych błędów w projekcie. Innym istotnym zagadnieniem jest czasochłonność procesu prototypowania; opóźnienia mogą wynikać z trudności w pozyskaniu odpowiednich materiałów lub technologii. Problemy z jakością komponentów również mogą wpłynąć na ostateczny efekt budowy maszyny; niskiej jakości części mogą prowadzić do awarii lub konieczności przeprowadzania dodatkowych prac naprawczych. Dodatkowo, zmiany w przepisach dotyczących bezpieczeństwa lub ochrony środowiska mogą wymusić modyfikacje już zaplanowanych rozwiązań, co generuje dodatkowe koszty i opóźnienia. Wreszcie, nieprzewidziane okoliczności, takie jak zmiany na rynku surowców czy problemy logistyczne, mogą wpłynąć na harmonogram realizacji projektu.
Jakie są zalety korzystania z symulacji komputerowych w projektowaniu maszyn
Symulacje komputerowe stały się nieodłącznym elementem procesu projektowania i budowy maszyn przemysłowych. Dzięki nim inżynierowie mogą przewidzieć zachowanie maszyny w różnych warunkach operacyjnych jeszcze przed jej fizycznym wykonaniem. To pozwala na identyfikację potencjalnych problemów oraz optymalizację konstrukcji bez ponoszenia kosztów związanych z prototypowaniem. Symulacje umożliwiają także przeprowadzanie testów obciążeniowych oraz analizę dynamiki ruchu, co jest szczególnie istotne w przypadku skomplikowanych układów mechanicznych. Dzięki wizualizacji wyników symulacji możliwe jest lepsze zrozumienie interakcji między różnymi komponentami maszyny oraz ich wpływu na ogólną wydajność urządzenia. Dodatkowo, wykorzystanie symulacji przyspiesza proces projektowania; inżynierowie mogą szybko testować różne warianty konstrukcyjne i wybierać te najbardziej optymalne.
Jakie są wyzwania związane z utrzymaniem maszyn przemysłowych
Utrzymanie maszyn przemysłowych to kluczowy aspekt zapewniający ciągłość produkcji oraz minimalizację przestojów. Jednym z głównych wyzwań jest konieczność regularnego monitorowania stanu technicznego urządzeń; wiele firm boryka się z brakiem odpowiednich narzędzi diagnostycznych lub wiedzy potrzebnej do skutecznego przeprowadzania konserwacji. Wprowadzenie nowoczesnych systemów monitorowania opartych na IoT może znacznie ułatwić ten proces poprzez zbieranie danych o stanie maszyny w czasie rzeczywistym i przewidywanie potencjalnych awarii przed ich wystąpieniem. Kolejnym wyzwaniem jest zarządzanie częściami zamiennymi; dostępność odpowiednich komponentów może być ograniczona przez długie czasy dostaw lub wysokie koszty zakupu. Warto również zwrócić uwagę na szkolenie personelu odpowiedzialnego za utrzymanie maszyn; brak odpowiednich umiejętności może prowadzić do błędów podczas konserwacji i napraw, co negatywnie wpływa na wydajność produkcji.
Jakie są przyszłościowe kierunki rozwoju technologii w budowie maszyn
Przyszłość technologii związanych z budową maszyn przemysłowych zapowiada się niezwykle obiecująco dzięki dynamicznemu rozwojowi innowacyjnych rozwiązań technologicznych. Jednym z najważniejszych kierunków rozwoju jest dalsza automatyzacja procesów produkcyjnych; roboty stają się coraz bardziej wszechstronne i zdolne do wykonywania skomplikowanych zadań wymagających precyzji i szybkości działania. Zastosowanie sztucznej inteligencji pozwala na optymalizację procesów produkcyjnych poprzez analizę danych oraz uczenie się na podstawie wcześniejszych doświadczeń. Również rozwój technologii druku 3D ma ogromny potencjał; umożliwia on szybkie prototypowanie oraz produkcję części zamiennych bez potrzeby stosowania tradycyjnych metod obróbczych. Zrównoważony rozwój staje się coraz bardziej istotny; producenci poszukują ekologicznych materiałów oraz rozwiązań pozwalających na redukcję zużycia energii i emisji CO2 podczas produkcji maszyn.