Budowa maszyn pneumatycznych opiera się na kilku kluczowych elementach, które współpracują ze sobą w celu efektywnego działania systemów wykorzystujących sprężone powietrze. Pierwszym z nich jest kompresor, który odpowiada za sprężanie powietrza i dostarczanie go do całego układu. Kompresory mogą mieć różne typy, takie jak tłokowe, śrubowe czy wirnikowe, a ich wybór zależy od specyfiki zastosowania oraz wymagań dotyczących ciśnienia i wydajności. Kolejnym istotnym elementem są zbiorniki ciśnieniowe, które służą do przechowywania sprężonego powietrza, co pozwala na stabilizację ciśnienia w systemie oraz zapewnia dostępność powietrza w momentach zwiększonego zapotrzebowania. Równie ważne są elementy sterujące, takie jak zawory, które regulują przepływ powietrza oraz jego kierunek. Zawory te mogą być ręczne lub automatyczne i mają kluczowe znaczenie dla precyzyjnego działania maszyny. Oprócz tego w budowie maszyn pneumatycznych nie można zapomnieć o siłownikach pneumatycznych, które przekształcają energię sprężonego powietrza w ruch mechaniczny, umożliwiając wykonywanie różnych zadań roboczych.
Jakie są zalety i wady maszyn pneumatycznych
Maszyny pneumatyczne mają wiele zalet, które sprawiają, że są szeroko stosowane w różnych branżach przemysłowych. Jedną z najważniejszych korzyści jest ich prostota konstrukcji oraz łatwość w obsłudze. Dzięki temu operatorzy mogą szybko nauczyć się ich używania, co przekłada się na mniejsze koszty szkolenia pracowników. Ponadto maszyny te charakteryzują się dużą niezawodnością i długowiecznością, co czyni je idealnym rozwiązaniem dla zakładów produkcyjnych wymagających ciągłej pracy. Inną istotną zaletą jest możliwość pracy w trudnych warunkach atmosferycznych oraz w środowiskach zanieczyszczonych, gdzie inne maszyny mogłyby ulegać awariom. Jednakże maszyny pneumatyczne mają również swoje ograniczenia. Przykładowo, ich wydajność może być niższa w porównaniu do maszyn elektrycznych czy hydraulicznych przy dużych obciążeniach. Dodatkowo sprężone powietrze jest mniej efektywne energetycznie niż inne źródła energii, co może prowadzić do wyższych kosztów eksploatacji.
Jakie zastosowania mają maszyny pneumatyczne w przemyśle
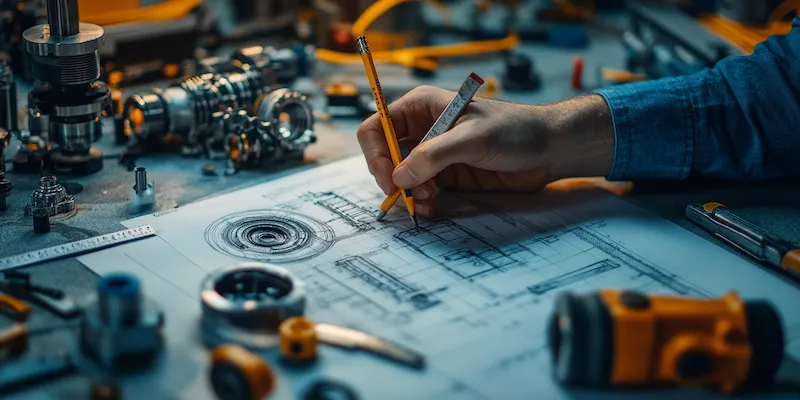
Budowa maszyn pneumatycznych
Maszyny pneumatyczne znajdują zastosowanie w wielu dziedzinach przemysłu dzięki swojej wszechstronności i efektywności działania. W przemyśle produkcyjnym wykorzystywane są do automatyzacji procesów montażowych oraz pakowania produktów. Siłowniki pneumatyczne umożliwiają szybkie i precyzyjne ruchy, co zwiększa wydajność linii produkcyjnych. W branży motoryzacyjnej maszyny te są używane do lakierowania pojazdów oraz do operacji związanych z obróbką metali. Dzięki zastosowaniu sprężonego powietrza można uzyskać wysoką jakość powierzchni oraz skrócić czas cyklu produkcyjnego. W logistyce maszyny pneumatyczne odgrywają kluczową rolę w systemach transportowych, gdzie stosowane są do podnoszenia i przenoszenia ciężkich ładunków. W sektorze budowlanym natomiast wykorzystuje się je do narzędzi takich jak młoty udarowe czy wiertarki pneumatyczne, które charakteryzują się dużą mocą i niezawodnością. Co więcej, maszyny pneumatyczne znajdują również zastosowanie w medycynie, gdzie używane są w urządzeniach do wentylacji pacjentów czy też w systemach dostarczania leków.
Jakie są nowoczesne technologie związane z maszynami pneumatycznymi
Nowoczesne technologie związane z maszynami pneumatycznymi rozwijają się dynamicznie i przyczyniają się do zwiększenia efektywności oraz bezpieczeństwa ich użytkowania. Jednym z najważniejszych trendów jest automatyzacja procesów przemysłowych poprzez integrację maszyn pneumatycznych z systemami sterowania opartymi na sztucznej inteligencji oraz Internetu Rzeczy (IoT). Dzięki temu możliwe jest zdalne monitorowanie stanu urządzeń oraz optymalizacja ich pracy na podstawie danych zbieranych w czasie rzeczywistym. Innowacyjne rozwiązania obejmują także zastosowanie materiałów kompozytowych i lekkich stopów metali w budowie komponentów maszyn pneumatycznych, co pozwala na zmniejszenie ich masy oraz zwiększenie wydajności energetycznej. Ponadto rozwijają się technologie filtracji powietrza oraz odzysku energii ze sprężonego powietrza, co przyczynia się do zmniejszenia kosztów eksploatacji tych urządzeń. Warto również zwrócić uwagę na postęp w zakresie rozwoju zaworów elektromagnetycznych oraz siłowników o zmiennej geometrii, które oferują większą precyzję działania i szybszą reakcję na zmiany warunków pracy.
Jakie są kluczowe aspekty bezpieczeństwa w maszynach pneumatycznych
Bezpieczeństwo w kontekście maszyn pneumatycznych jest niezwykle istotnym zagadnieniem, które powinno być traktowane priorytetowo na każdym etapie ich użytkowania. W pierwszej kolejności należy zwrócić uwagę na odpowiednie szkolenie pracowników, którzy będą obsługiwać te maszyny. Szkolenia powinny obejmować nie tylko zasady działania urządzeń, ale także procedury awaryjne oraz sposoby minimalizacji ryzyka. Ważnym elementem jest również regularna konserwacja i inspekcja maszyn, co pozwala na wczesne wykrywanie potencjalnych usterek i zapobieganie wypadkom. Kolejnym kluczowym aspektem jest stosowanie odpowiednich zabezpieczeń, takich jak osłony mechaniczne oraz systemy blokad, które uniemożliwiają przypadkowe uruchomienie maszyny w trakcie jej serwisowania. Należy także zadbać o właściwe oznakowanie strefy pracy maszyn pneumatycznych oraz informowanie pracowników o potencjalnych zagrożeniach związanych z ich obsługą. Warto również inwestować w nowoczesne technologie monitorujące, które mogą automatycznie wykrywać nieprawidłowości w działaniu maszyn i informować operatorów o konieczności podjęcia działań naprawczych.
Jakie są trendy w rozwoju maszyn pneumatycznych na rynku
W ostatnich latach rynek maszyn pneumatycznych przeszedł wiele zmian, a nowe trendy wskazują na rosnącą innowacyjność oraz adaptację do potrzeb współczesnego przemysłu. Jednym z najważniejszych trendów jest dążenie do zwiększenia efektywności energetycznej tych urządzeń. Producenci coraz częściej inwestują w technologie umożliwiające odzysk energii ze sprężonego powietrza oraz optymalizację procesów sprężania, co pozwala na redukcję kosztów eksploatacyjnych. Innym istotnym kierunkiem rozwoju jest miniaturyzacja komponentów pneumatycznych, co umożliwia ich zastosowanie w bardziej zaawansowanych aplikacjach oraz w miejscach o ograniczonej przestrzeni. Wzrost znaczenia automatyzacji i robotyzacji procesów produkcyjnych również wpływa na rozwój maszyn pneumatycznych, które muszą być kompatybilne z nowoczesnymi systemami sterowania i komunikacji. Warto również zauważyć rosnącą popularność rozwiązań mobilnych i przenośnych, które umożliwiają elastyczne wykorzystanie technologii pneumatycznej w różnych warunkach pracy. Na rynku pojawiają się także innowacyjne materiały i technologie produkcji, które zwiększają trwałość i niezawodność elementów pneumatycznych.
Jakie są różnice między maszynami pneumatycznymi a hydraulicznymi
Maszyny pneumatyczne i hydrauliczne to dwa różne typy systemów mechanicznych, które mają swoje unikalne cechy oraz zastosowania. Główna różnica między nimi polega na medium roboczym: maszyny pneumatyczne wykorzystują sprężone powietrze, podczas gdy maszyny hydrauliczne działają na zasadzie ciśnienia cieczy hydraulicznej. Dzięki temu maszyny pneumatyczne są zazwyczaj lżejsze i prostsze w budowie, co sprawia, że są łatwiejsze do transportu i instalacji. Z drugiej strony maszyny hydrauliczne oferują znacznie większą moc i moment obrotowy przy mniejszych rozmiarach, co czyni je bardziej odpowiednimi do zadań wymagających dużych sił roboczych. W kontekście kosztów eksploatacji warto zauważyć, że systemy pneumatyczne są często tańsze w utrzymaniu ze względu na mniejsze ryzyko wycieków oraz prostszą konstrukcję układów sterujących. Jednakże sprężone powietrze jest mniej efektywne energetycznie niż ciecz hydrauliczna, co może prowadzić do wyższych kosztów operacyjnych przy dużych obciążeniach.
Jakie są najczęstsze problemy związane z maszynami pneumatycznymi
Maszyny pneumatyczne, mimo swoich licznych zalet, mogą napotykać różnorodne problemy podczas eksploatacji. Jednym z najczęstszych problemów są wycieki sprężonego powietrza, które mogą prowadzić do obniżenia wydajności całego systemu oraz zwiększenia kosztów eksploatacyjnych. Wycieki mogą występować na różnych elementach układu, takich jak przewody czy zawory, dlatego regularna inspekcja i konserwacja są kluczowe dla ich eliminacji. Innym powszechnym problemem jest niewłaściwe ciśnienie robocze, które może wynikać z uszkodzenia kompresora lub niewłaściwego ustawienia zaworów regulacyjnych. Niewłaściwe ciśnienie może prowadzić do spadku wydajności maszyny lub nawet jej uszkodzenia. Dodatkowo zanieczyszczenia powietrza mogą wpływać negatywnie na działanie układów pneumatycznych, dlatego ważne jest stosowanie filtrów powietrza oraz regularne ich czyszczenie lub wymiana. Problemy mogą także wynikać z niewłaściwego użytkowania maszyn przez operatorów, dlatego tak ważne jest przeprowadzanie szkoleń dotyczących obsługi urządzeń oraz zasad bezpieczeństwa.
Jakie są przyszłościowe kierunki rozwoju technologii pneumatycznych
Przyszłość technologii pneumatycznych zapowiada się obiecująco dzięki ciągłemu postępowi technologicznemu oraz rosnącemu zapotrzebowaniu na automatyzację procesów przemysłowych. Jednym z kluczowych kierunków rozwoju będzie dalsza integracja systemów pneumatycznych z technologią IoT, co umożliwi zdalne monitorowanie stanu urządzeń oraz optymalizację ich pracy na podstawie danych zbieranych w czasie rzeczywistym. Dzięki temu możliwe będzie przewidywanie awarii oraz planowanie konserwacji jeszcze przed wystąpieniem problemu. Również rozwój sztucznej inteligencji może przyczynić się do poprawy efektywności działania systemów pneumatycznych poprzez automatyczne dostosowywanie parametrów pracy do zmieniających się warunków otoczenia czy obciążenia roboczego. Innowacje materiałowe będą miały znaczący wpływ na trwałość i niezawodność komponentów pneumatycznych; zastosowanie nowych materiałów kompozytowych może przyczynić się do zmniejszenia masy urządzeń oraz zwiększenia ich odporności na korozję czy uszkodzenia mechaniczne. Wreszcie rosnące zainteresowanie ekologicznymi rozwiązaniami sprawi, że producenci będą poszukiwać sposobów na zmniejszenie zużycia energii oraz emisji hałasu związanej z pracą maszyn pneumatycznych.