Automatyzacja linii technologicznych w przemyśle przynosi wiele korzyści, które mają znaczący wpływ na efektywność produkcji oraz jakość wyrobów. Przede wszystkim, automatyzacja pozwala na zwiększenie wydajności procesów produkcyjnych. Dzięki zastosowaniu nowoczesnych systemów sterowania i robotyzacji, przedsiębiorstwa mogą znacznie przyspieszyć tempo produkcji, co przekłada się na większą ilość wyprodukowanych towarów w krótszym czasie. Kolejną zaletą jest poprawa jakości produktów. Automatyczne systemy są w stanie utrzymać stałe parametry produkcji, co minimalizuje ryzyko błędów ludzkich oraz zapewnia jednolitą jakość wyrobów. Dodatkowo, automatyzacja przyczynia się do redukcji kosztów operacyjnych. Mniejsze zapotrzebowanie na pracowników w niektórych obszarach produkcji pozwala na ograniczenie wydatków związanych z wynagrodzeniami oraz szkoleniami. Warto również zauważyć, że automatyzacja sprzyja zwiększeniu bezpieczeństwa pracy, ponieważ wiele niebezpiecznych zadań może być wykonywanych przez maszyny, co zmniejsza ryzyko wypadków w miejscu pracy.
Jakie technologie są wykorzystywane w automatyzacji linii produkcyjnych
W automatyzacji linii technologicznych dla przemysłu wykorzystuje się szereg nowoczesnych technologii, które wspierają procesy produkcyjne i zwiększają ich efektywność. Jednym z kluczowych elementów są systemy sterowania PLC (Programmable Logic Controller), które umożliwiają precyzyjne zarządzanie maszynami i procesami technologicznymi. Dzięki nim można programować różne scenariusze działania maszyn oraz monitorować ich stan w czasie rzeczywistym. Inną istotną technologią są roboty przemysłowe, które wykonują powtarzalne zadania z dużą dokładnością i szybkością. Robotyzacja pozwala na zwiększenie wydajności oraz elastyczności produkcji, a także na redukcję kosztów pracy. W ostatnich latach coraz większą rolę odgrywają także systemy sztucznej inteligencji i uczenia maszynowego, które analizują dane z procesu produkcyjnego i optymalizują go na bieżąco. Dodatkowo, Internet Rzeczy (IoT) umożliwia zbieranie danych z różnych urządzeń oraz ich analizę w celu poprawy efektywności operacyjnej.
Jakie wyzwania wiążą się z automatyzacją linii technologicznych
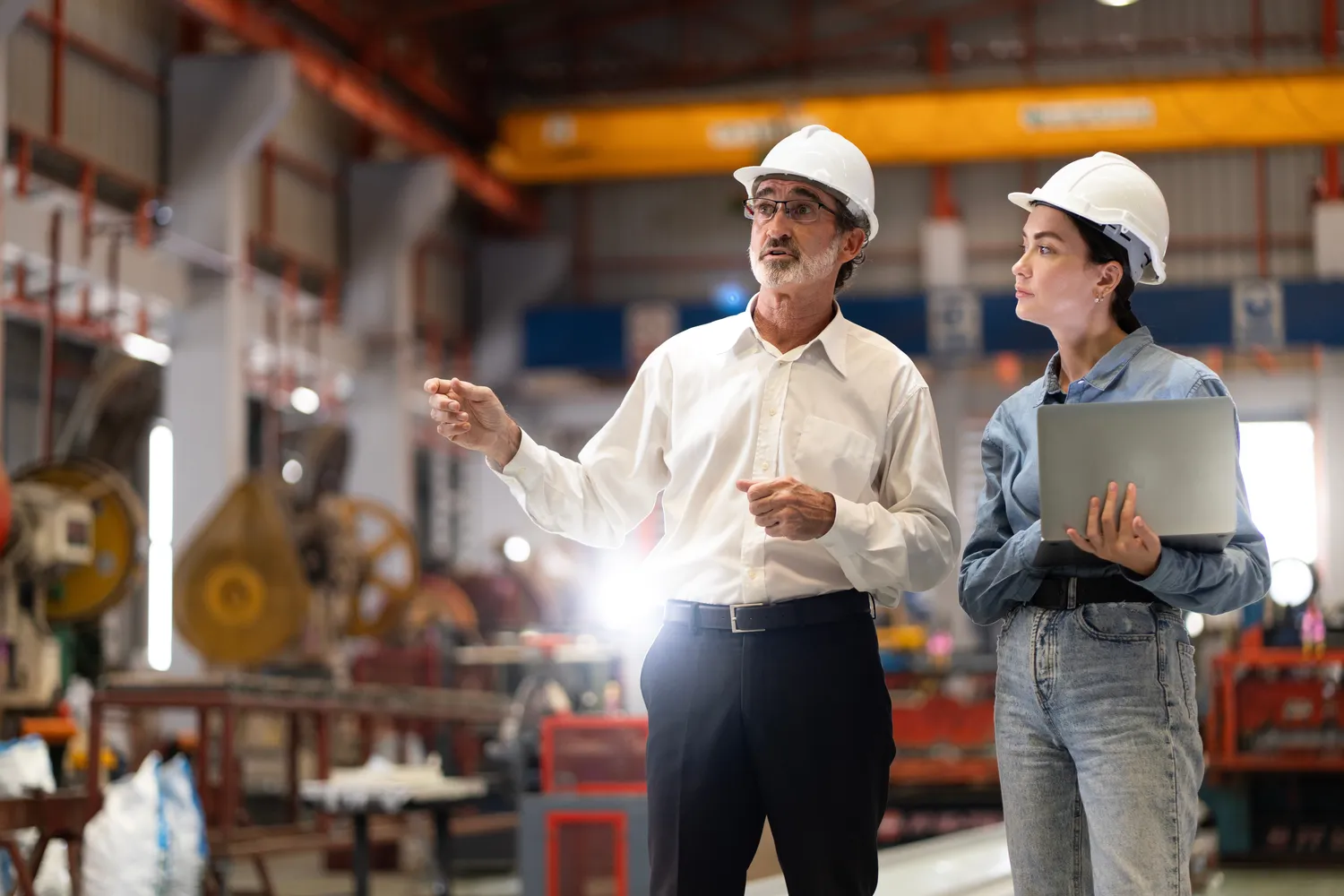
Automatyzacja linii technologicznych dla przemysłu
Automatyzacja linii technologicznych w przemyśle niesie ze sobą wiele korzyści, ale również stawia przed przedsiębiorstwami szereg wyzwań. Jednym z głównych problemów jest wysoki koszt początkowy związany z inwestycjami w nowoczesne technologie oraz infrastrukturę. Przemiany te wymagają znacznych nakładów finansowych na zakup maszyn, oprogramowania oraz szkolenia pracowników. Kolejnym wyzwaniem jest konieczność dostosowania procesów produkcyjnych do nowych technologii, co często wiąże się z reorganizacją całej struktury zakładu. Wprowadzenie automatyzacji może również spotkać się z oporem ze strony pracowników obawiających się utraty pracy lub konieczności nauki nowych umiejętności. Ważnym aspektem jest także zapewnienie odpowiedniego poziomu bezpieczeństwa danych oraz ochrony przed cyberatakami, które mogą stanowić zagrożenie dla funkcjonowania zautomatyzowanych systemów. Dodatkowo, przedsiębiorstwa muszą być przygotowane na ciągłe aktualizacje i konserwację sprzętu oraz oprogramowania, aby utrzymać wysoką wydajność i niezawodność linii produkcyjnych.
Jak wdrożyć automatyzację linii technologicznych krok po kroku
Wdrożenie automatyzacji linii technologicznych dla przemysłu wymaga starannego planowania oraz realizacji kilku kluczowych kroków. Pierwszym etapem jest analiza obecnych procesów produkcyjnych oraz identyfikacja obszarów, które mogą zostać zoptymalizowane poprzez automatyzację. Ważne jest również określenie celów biznesowych związanych z wdrożeniem nowych technologii, takich jak zwiększenie wydajności czy poprawa jakości produktów. Następnie należy przeprowadzić badania rynku w celu wyboru odpowiednich rozwiązań technologicznych oraz dostawców sprzętu i oprogramowania. Po dokonaniu wyboru warto stworzyć szczegółowy plan wdrożenia, który uwzględni harmonogram działań oraz budżet projektu. Kluczowym krokiem jest także zaangażowanie zespołu pracowników w proces zmian poprzez szkolenia i warsztaty, które pomogą im dostosować się do nowych warunków pracy. Po zakończeniu etapu wdrożenia ważne jest monitorowanie wyników i efektywności nowego systemu oraz dokonywanie ewentualnych korekt w celu dalszej optymalizacji procesów produkcyjnych.
Jakie są przykłady zastosowania automatyzacji w różnych branżach przemysłowych
Automatyzacja linii technologicznych znajduje zastosowanie w wielu branżach przemysłowych, co pozwala na zwiększenie efektywności oraz poprawę jakości produkcji. W przemyśle motoryzacyjnym roboty przemysłowe są wykorzystywane do montażu pojazdów, gdzie precyzyjne i szybkie wykonanie zadań jest kluczowe. Automatyzacja procesów spawania, malowania oraz montażu komponentów pozwala na znaczne skrócenie czasu produkcji oraz redukcję błędów. W branży spożywczej automatyzacja obejmuje zarówno procesy pakowania, jak i sortowania produktów. Zastosowanie nowoczesnych maszyn do pakowania pozwala na zwiększenie wydajności oraz zapewnienie wysokiej jakości opakowań, co jest istotne dla zachowania świeżości żywności. W przemyśle elektronicznym automatyzacja linii produkcyjnych umożliwia masową produkcję skomplikowanych podzespołów z zachowaniem wysokiej precyzji. Dzięki zastosowaniu technologii pick-and-place roboty mogą szybko i dokładnie przenosić elementy na liniach montażowych. W sektorze farmaceutycznym automatyzacja jest niezbędna do zapewnienia zgodności z rygorystycznymi normami jakości i bezpieczeństwa. Systemy automatyzacji monitorują procesy produkcyjne, co pozwala na ścisłą kontrolę jakości oraz minimalizację ryzyka zanieczyszczenia produktów.
Jakie są przyszłe trendy w automatyzacji linii technologicznych
Przemysł 4.0 wprowadza nowe trendy w automatyzacji linii technologicznych, które mają potencjał do zrewolucjonizowania sposobu produkcji. Jednym z najważniejszych trendów jest rozwój sztucznej inteligencji i uczenia maszynowego, które umożliwiają systemom automatycznym samodzielne podejmowanie decyzji na podstawie analizy danych. Dzięki temu możliwe jest optymalizowanie procesów w czasie rzeczywistym oraz przewidywanie awarii maszyn, co znacząco zwiększa efektywność produkcji. Kolejnym istotnym trendem jest integracja Internetu Rzeczy (IoT) z systemami automatyzacji, co pozwala na zbieranie danych z różnych urządzeń i ich analizę w celu poprawy wydajności operacyjnej. Dzięki IoT przedsiębiorstwa mogą monitorować stan maszyn oraz zużycie surowców w czasie rzeczywistym, co umożliwia szybsze reagowanie na zmiany w procesie produkcyjnym. Również rozwój technologii chmurowych staje się coraz bardziej popularny, umożliwiając przedsiębiorstwom dostęp do zaawansowanych narzędzi analitycznych oraz elastyczne zarządzanie danymi. Warto również zwrócić uwagę na rosnącą rolę robotyzacji współpracującej, gdzie roboty pracują obok ludzi, wspierając ich w wykonywaniu zadań bez konieczności pełnej automatyzacji procesu.
Jakie umiejętności są potrzebne do pracy w obszarze automatyzacji
W miarę jak automatyzacja linii technologicznych staje się coraz bardziej powszechna, rośnie zapotrzebowanie na specjalistów posiadających odpowiednie umiejętności w tym obszarze. Kluczową kompetencją jest znajomość programowania systemów sterujących oraz robotów przemysłowych. Osoby pracujące w tej dziedzinie powinny być biegłe w językach programowania takich jak Python czy C++, a także znać specyfikacje dotyczące systemów PLC i SCADA. Ważna jest również umiejętność analizy danych oraz znajomość narzędzi do wizualizacji danych, ponieważ wiele procesów automatycznych opiera się na analizie dużych zbiorów informacji. Dodatkowo, inżynierowie zajmujący się automatyką muszą mieć wiedzę z zakresu mechaniki i elektroniki, aby móc skutecznie projektować i wdrażać rozwiązania techniczne. Umiejętności interpersonalne są równie istotne; zdolność do pracy zespołowej oraz komunikacji z innymi działami firmy jest kluczowa dla skutecznego wdrażania projektów automatyzacyjnych.
Jakie są koszty związane z wdrożeniem automatyzacji linii technologicznych
Koszty związane z wdrożeniem automatyzacji linii technologicznych mogą być znaczne i różnią się w zależności od specyfiki branży oraz zakresu projektu. Na początku należy uwzględnić inwestycje w sprzęt i technologie, które mogą obejmować zakup robotów przemysłowych, systemów sterujących oraz oprogramowania do zarządzania procesami produkcyjnymi. Koszt zakupu nowoczesnych maszyn może być bardzo wysoki, zwłaszcza gdy mowa o zaawansowanych rozwiązaniach dostosowanych do specyficznych potrzeb przedsiębiorstwa. Kolejnym istotnym elementem budżetu są wydatki związane z instalacją i uruchomieniem nowych systemów, które mogą wymagać wsparcia ze strony specjalistycznych firm inżynieryjnych lub konsultantów. Nie można zapominać o kosztach szkoleń dla pracowników, którzy muszą nauczyć się obsługi nowych technologii oraz dostosować swoje umiejętności do zmieniających się warunków pracy. Dodatkowo warto uwzględnić koszty utrzymania systemów automatycznych, które mogą obejmować konserwację sprzętu oraz aktualizacje oprogramowania.
Jakie są najlepsze praktyki przy wdrażaniu automatyzacji
Aby skutecznie wdrożyć automatyzację linii technologicznych w przemyśle, warto kierować się kilkoma najlepszymi praktykami. Po pierwsze, kluczowe jest przeprowadzenie dokładnej analizy potrzeb przedsiębiorstwa oraz identyfikacja obszarów wymagających optymalizacji poprzez automatyzację. Należy jasno określić cele projektu oraz oczekiwane rezultaty, co pozwoli na lepsze zarządzanie procesem wdrożenia. Ważne jest także zaangażowanie zespołu pracowników od samego początku projektu; ich wiedza i doświadczenie mogą okazać się nieocenione podczas planowania i realizacji działań związanych z automatyzacją. Kolejną praktyką jest wybór odpowiednich technologii i dostawców; warto przeanalizować dostępne rozwiązania rynkowe oraz porównać oferty różnych firm przed podjęciem decyzji o zakupie sprzętu czy oprogramowania. Po wdrożeniu systemu niezwykle istotne jest monitorowanie jego efektywności oraz regularne dokonywanie aktualizacji i konserwacji sprzętu; dzięki temu można zapewnić ciągłość działania linii produkcyjnej oraz maksymalną wydajność procesów.