Destylacja rozpuszczalników to proces, który polega na oddzieleniu substancji na podstawie różnicy w ich temperaturach wrzenia. W praktyce oznacza to, że ciecz, która ma niższą temperaturę wrzenia, odparowuje jako pierwsza, a następnie skrapla się w innym miejscu, tworząc czystszy produkt. Proces ten jest szeroko stosowany w przemyśle chemicznym oraz farmaceutycznym do oczyszczania substancji i uzyskiwania wysokiej jakości rozpuszczalników. W destylacji rozpuszczalników kluczowe są odpowiednie warunki, takie jak ciśnienie atmosferyczne oraz temperatura, które wpływają na efektywność procesu. W zależności od rodzaju rozpuszczalnika oraz pożądanej czystości końcowego produktu, można zastosować różne metody destylacji, takie jak destylacja prosta, frakcyjna czy też destylacja pod ciśnieniem.
Jakie są główne metody destylacji rozpuszczalników
W kontekście destylacji rozpuszczalników wyróżniamy kilka podstawowych metod, które różnią się między sobą zastosowaniem oraz efektywnością. Destylacja prosta jest najczęściej stosowaną metodą, polegającą na podgrzewaniu mieszaniny cieczy i zbieraniu pary, która skrapla się w chłodnicy. Jest to metoda stosunkowo łatwa do przeprowadzenia, jednak jej skuteczność maleje w przypadku mieszanin o zbliżonych temperaturach wrzenia. W takich sytuacjach lepszym rozwiązaniem jest destylacja frakcyjna, która pozwala na bardziej precyzyjne oddzielenie składników dzięki zastosowaniu kolumny frakcyjnej. Ta metoda umożliwia wielokrotne skraplanie i odparowywanie pary, co zwiększa czystość uzyskiwanego produktu. Innym podejściem jest destylacja pod ciśnieniem, która pozwala na obniżenie temperatury wrzenia substancji poprzez zwiększenie ciśnienia.
Jakie są zastosowania destylacji rozpuszczalników w przemyśle
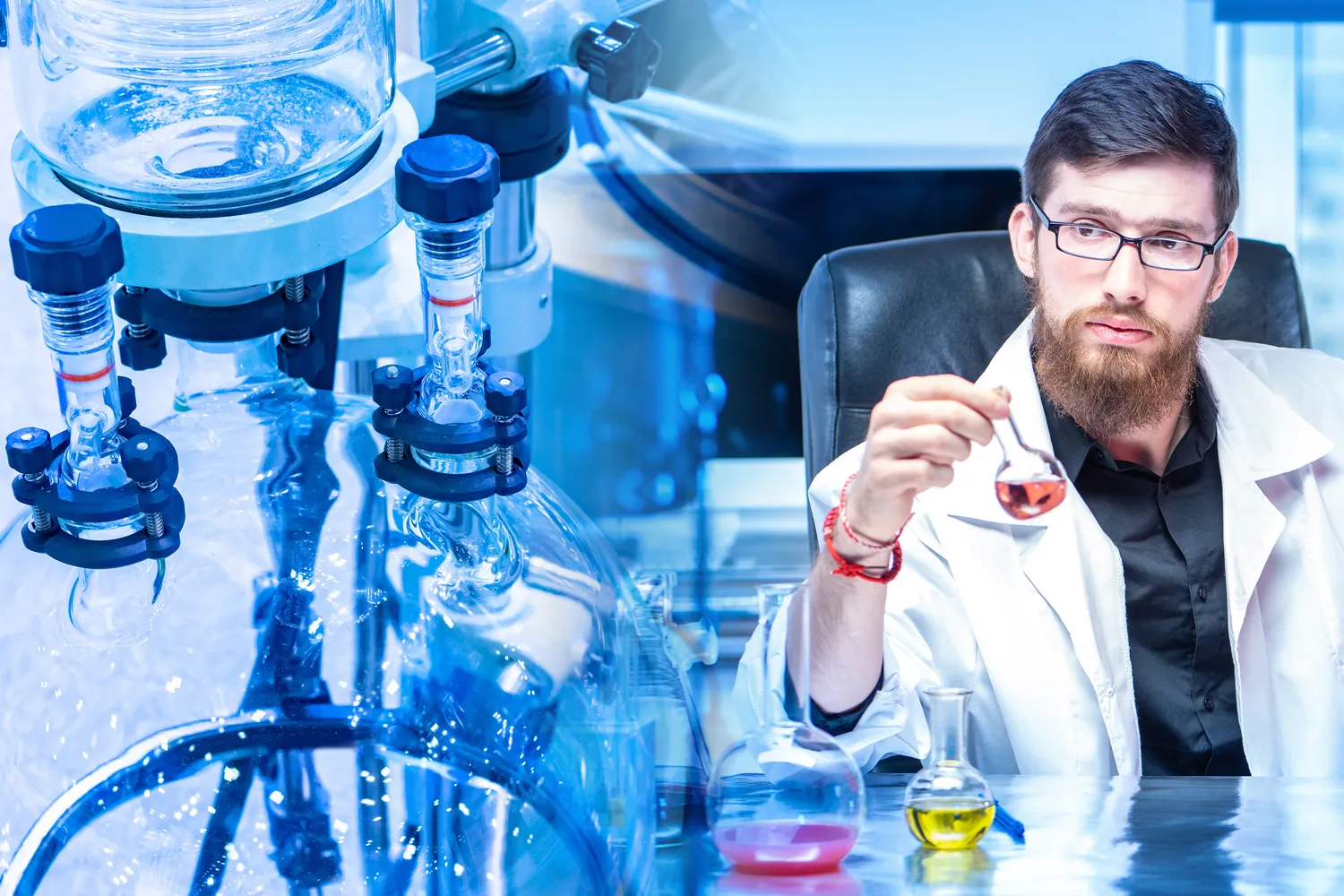
Destylacja rozpuszczalników
Destylacja rozpuszczalników znajduje szerokie zastosowanie w różnych gałęziach przemysłu. W przemyśle chemicznym proces ten jest kluczowy dla produkcji wielu substancji chemicznych oraz ich oczyszczania. Dzięki destylacji można uzyskać wysokiej jakości rozpuszczalniki organiczne, które są niezbędne w syntezach chemicznych oraz procesach produkcyjnych. Również w przemyśle farmaceutycznym destylacja odgrywa istotną rolę w produkcji leków oraz substancji czynnych. Oczyszczanie surowców chemicznych za pomocą tego procesu pozwala na uzyskanie produktów o wysokiej czystości i stabilności. Ponadto destylacja jest wykorzystywana w produkcji alkoholi oraz napojów spirytusowych, gdzie kluczowe jest oddzielenie etanolu od innych składników. W branży petrochemicznej proces ten służy do rafinacji ropy naftowej i uzyskiwania różnych frakcji paliwowych.
Jakie są korzyści z użycia destylacji rozpuszczalników
Korzystanie z destylacji rozpuszczalników niesie ze sobą wiele korzyści zarówno dla producentów, jak i dla konsumentów. Przede wszystkim proces ten umożliwia uzyskanie czystych substancji chemicznych, co jest niezwykle istotne w kontekście jakości produktów końcowych. Wysoka czystość surowców przekłada się na lepsze właściwości fizykochemiczne oraz większą stabilność produktów finalnych. Dodatkowo destylacja pozwala na efektywne odzyskiwanie cennych surowców z odpadów przemysłowych, co przyczynia się do zmniejszenia kosztów produkcji oraz ochrony środowiska. Dzięki temu przedsiębiorstwa mogą działać bardziej ekologicznie i zgodnie z zasadami zrównoważonego rozwoju. Kolejną zaletą jest możliwość dostosowania procesu do specyficznych potrzeb danej branży lub produktu, co sprawia, że destylacja jest niezwykle wszechstronnym narzędziem w rękach inżynierów chemików.
Jakie są wyzwania związane z destylacją rozpuszczalników
Destylacja rozpuszczalników, mimo swoich licznych zalet, wiąże się również z pewnymi wyzwaniami, które mogą wpływać na efektywność i koszty procesu. Jednym z głównych problemów jest konieczność precyzyjnego kontrolowania temperatury oraz ciśnienia w trakcie destylacji. Niewłaściwe ustawienia mogą prowadzić do niepełnego oddzielenia składników, co skutkuje obniżoną jakością uzyskiwanego produktu. Ponadto, w przypadku mieszanin o bliskich temperaturach wrzenia, proces może być czasochłonny i kosztowny, co wymaga zastosowania bardziej zaawansowanych technologii, takich jak kolumny frakcyjne. Kolejnym wyzwaniem jest kwestia bezpieczeństwa, zwłaszcza w kontekście pracy z substancjami łatwopalnymi lub toksycznymi. Odpowiednie zabezpieczenia oraz procedury operacyjne muszą być wdrożone, aby zminimalizować ryzyko wypadków. Wreszcie, destylacja może generować znaczną ilość odpadów, co stawia przed przemysłem wymagania dotyczące ich utylizacji i recyklingu.
Jakie są nowoczesne technologie w destylacji rozpuszczalników
W ostatnich latach nastąpił znaczny rozwój technologii związanych z destylacją rozpuszczalników, co przyczyniło się do zwiększenia efektywności i oszczędności tego procesu. Jednym z najważniejszych osiągnięć jest zastosowanie technologii membranowych, które pozwalają na separację składników bez potrzeby podgrzewania ich do wysokich temperatur. Dzięki temu można zaoszczędzić energię oraz zminimalizować ryzyko degradacji wrażliwych substancji chemicznych. Innym innowacyjnym rozwiązaniem są kolumny destylacyjne o wysokiej wydajności, które umożliwiają bardziej efektywne oddzielanie składników dzięki zastosowaniu zaawansowanych materiałów i konstrukcji. Wprowadzenie automatyzacji i systemów monitoringu pozwala na bieżące śledzenie parametrów procesu oraz szybką reakcję na ewentualne nieprawidłowości. Dodatkowo rozwijają się technologie związane z odzyskiem ciepła, które pozwalają na ponowne wykorzystanie energii w procesie destylacji.
Jakie są różnice między destylacją a innymi metodami separacji
Destylacja rozpuszczalników to tylko jedna z wielu metod separacji składników mieszanin chemicznych. Warto porównać ją z innymi technikami, aby lepiej zrozumieć jej unikalne cechy oraz zastosowania. Na przykład ekstrakcja to proces polegający na przenoszeniu substancji rozpuszczonej z jednej fazy do drugiej, zazwyczaj przy użyciu rozpuszczalnika. Ekstrakcja może być bardziej efektywna w przypadku substancji o niskich temperaturach wrzenia lub tych, które są wrażliwe na wysoką temperaturę. Z kolei chromatografia to technika separacyjna oparta na różnicy w powinowactwie składników do fazy stacjonarnej i ruchomej. Jest to metoda niezwykle precyzyjna, ale często bardziej czasochłonna i kosztowna niż destylacja. Filtracja to kolejna technika separacji, która polega na oddzieleniu ciał stałych od cieczy poprzez przepuszczenie ich przez materiał filtracyjny. Choć filtracja jest prostsza i szybsza w wielu przypadkach, nie nadaje się do separacji cieczy o podobnych właściwościach fizykochemicznych.
Jakie są przyszłe kierunki rozwoju technologii destylacji
Przyszłość technologii destylacji rozpuszczalników wydaje się obiecująca, zwłaszcza w kontekście rosnących wymagań dotyczących efektywności energetycznej oraz ochrony środowiska. W miarę jak przemysł chemiczny staje przed wyzwaniami związanymi ze zmianami klimatycznymi i ograniczeniami zasobów naturalnych, innowacje w dziedzinie destylacji będą kluczowe dla zapewnienia zrównoważonego rozwoju. Wśród przyszłych kierunków rozwoju można wymienić dalsze badania nad technologiami membranowymi oraz ich zastosowaniem w procesach separacyjnych. Rozwój materiałów nanostrukturalnych może przyczynić się do zwiększenia efektywności procesów separacyjnych poprzez poprawę selektywności i wydajności membran. Ponadto automatyzacja procesów produkcyjnych będzie miała kluczowe znaczenie dla zwiększenia wydajności oraz redukcji kosztów operacyjnych. Integracja sztucznej inteligencji i uczenia maszynowego w monitorowaniu i optymalizacji procesów destylacji może prowadzić do znacznych oszczędności czasu i zasobów.
Jakie są przykłady zastosowań destylacji w laboratoriach
Destylacja rozpuszczalników znajduje szerokie zastosowanie nie tylko w przemyśle, ale także w laboratoriach badawczych i analitycznych. W laboratoriach chemicznych często stosuje się destylację do oczyszczania reagentów oraz produktów reakcji chemicznych. Dzięki temu naukowcy mogą uzyskać substancje o wysokiej czystości, co jest kluczowe dla przeprowadzania dokładnych badań oraz eksperymentów. Destylacja jest również wykorzystywana do analizy składu chemicznego różnych próbek poprzez oddzielanie poszczególnych składników przed ich dalszym badaniem za pomocą technik chromatograficznych czy spektroskopowych. W laboratoriach farmaceutycznych proces ten jest istotny dla produkcji leków oraz substancji czynnych o wymaganej czystości i stabilności.
Jakie są najczęściej stosowane aparaty do destylacji
Aparatura wykorzystywana do destylacji rozpuszczalników jest różnorodna i dostosowana do specyfiki danego procesu oraz wymagań jakościowych uzyskiwanego produktu. Najpopularniejszym urządzeniem jest klasyczna kolumna destylacyjna, która składa się z pionowej rurki wyposażonej w elementy wspomagające kondensację pary oraz zbieranie skroplin. Kolumny te mogą mieć różną długość i średnicę w zależności od potrzeb procesu frakcyjnego lub prostej destylacji. Inne istotne urządzenia to aparaty do destylacji rotacyjnej, które umożliwiają przeprowadzanie procesu pod zmniejszonym ciśnieniem, co pozwala na obniżenie temperatury wrzenia substancji i minimalizację ryzyka ich degradacji. Destylatory próżniowe są również powszechnie stosowane w laboratoriach chemicznych do oczyszczania cennych substancji organicznych czy farmaceutycznych.