Destylator przemysłowy to urządzenie służące do separacji składników mieszanin cieczy na podstawie różnic w ich temperaturach wrzenia. Proces destylacji polega na podgrzewaniu cieczy, co prowadzi do odparowania jej składników, a następnie skraplaniu pary w celu uzyskania czystych substancji. W przemyśle destylatory są wykorzystywane w różnych dziedzinach, takich jak produkcja alkoholu, petrochemia czy farmaceutyka. Istnieją różne rodzaje destylatorów, w tym destylatory prostokątne, kolumnowe oraz frakcyjne, które różnią się konstrukcją i zastosowaniem. W przypadku destylacji frakcyjnej, proces ten pozwala na oddzielenie wielu składników z jednego surowca, co czyni go niezwykle efektywnym w przemyśle chemicznym. Warto również zauważyć, że destylatory przemysłowe mogą być zautomatyzowane, co zwiększa ich wydajność i precyzję działania.
Jakie są zastosowania destylatorów przemysłowych w różnych branżach
Destylatory przemysłowe znajdują szerokie zastosowanie w wielu branżach, co sprawia, że są one kluczowym elementem wielu procesów produkcyjnych. W przemyśle spożywczym destylatory są wykorzystywane do produkcji alkoholu, takiego jak whisky czy wódka, gdzie proces destylacji pozwala na uzyskanie wysokiej jakości trunków o odpowiedniej mocy i smaku. W branży petrochemicznej destylatory służą do separacji różnych frakcji ropy naftowej, co umożliwia produkcję paliw oraz innych chemikaliów. W farmaceutyce natomiast destylacja jest stosowana do oczyszczania substancji czynnych oraz rozpuszczalników, co jest niezbędne dla zapewnienia bezpieczeństwa i skuteczności leków. Ponadto destylatory są także wykorzystywane w procesach recyklingu oraz oczyszczania ścieków, gdzie pozwalają na odzyskiwanie cennych surowców oraz minimalizację wpływu na środowisko.
Jakie są różnice między różnymi typami destylatorów przemysłowych
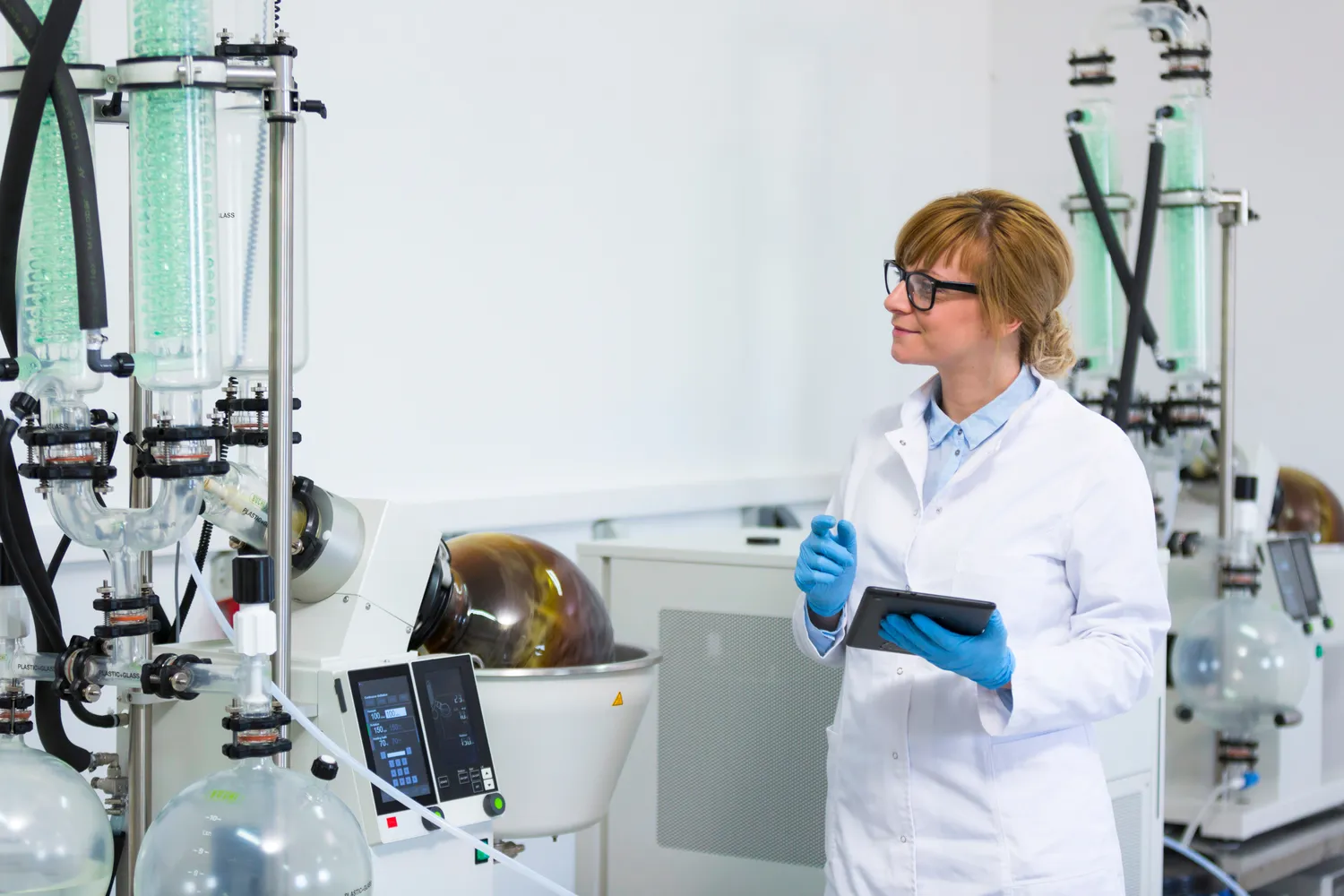
Destylator przemysłowy
Wybór odpowiedniego typu destylatora przemysłowego ma kluczowe znaczenie dla efektywności procesu produkcji. Istnieje kilka głównych typów destylatorów, które różnią się konstrukcją oraz sposobem działania. Destylatory prostokątne są najprostsze w budowie i często stosowane do podstawowych procesów destylacji. Charakteryzują się one niską wydajnością i są idealne do małych partii produkcyjnych. Z kolei destylatory kolumnowe są bardziej zaawansowane technologicznie i pozwalają na ciągłą produkcję dużych ilości substancji. Dzięki zastosowaniu kolumny frakcyjnej możliwe jest oddzielanie wielu składników jednocześnie, co zwiększa wydajność procesu. Innym rodzajem są destylatory frakcyjne, które umożliwiają bardziej skomplikowane separacje dzięki zastosowaniu wielu poziomych sekcji wewnątrz kolumny.
Jakie są kluczowe czynniki wpływające na wydajność destylatora przemysłowego
Wydajność destylatora przemysłowego zależy od wielu czynników, które mogą znacząco wpłynąć na efektywność całego procesu. Jednym z najważniejszych aspektów jest temperatura podgrzewania cieczy, która musi być odpowiednio dobrana do właściwości chemicznych składników mieszanki. Zbyt niska temperatura może prowadzić do niepełnej separacji substancji, podczas gdy zbyt wysoka może powodować niepożądane reakcje chemiczne. Kolejnym istotnym czynnikiem jest ciśnienie panujące w systemie; zmiany ciśnienia mogą wpływać na temperatury wrzenia poszczególnych składników i tym samym na efektywność procesu. Również konstrukcja samego urządzenia ma znaczenie; odpowiednia liczba poziomych sekcji w kolumnie frakcyjnej może zwiększyć powierzchnię kontaktu między parą a cieczą, co sprzyja lepszej separacji składników.
Jakie są najnowsze technologie stosowane w budowie destylatorów przemysłowych
W ostatnich latach nastąpił znaczny postęp technologiczny w dziedzinie budowy destylatorów przemysłowych, co przyczyniło się do zwiększenia ich wydajności oraz efektywności energetycznej. Nowoczesne urządzenia często wykorzystują zaawansowane materiały izolacyjne oraz technologie odzysku ciepła, co pozwala na zmniejszenie zużycia energii podczas procesu destylacji. Ponadto wiele nowoczesnych systemów wyposażonych jest w automatyczne systemy monitorowania i kontroli parametrów pracy, co umożliwia bieżące dostosowywanie warunków procesu do zmieniających się potrzeb produkcyjnych. Innowacyjne rozwiązania obejmują także zastosowanie sztucznej inteligencji oraz algorytmów uczenia maszynowego do optymalizacji procesów produkcyjnych oraz przewidywania ewentualnych awarii urządzeń.
Jakie są koszty związane z zakupem i eksploatacją destylatorów przemysłowych
Koszty zakupu i eksploatacji destylatorów przemysłowych mogą być znaczne, a ich wysokość zależy od wielu czynników, takich jak typ urządzenia, jego wydajność oraz zastosowane technologie. Zakup nowego destylatora to często inwestycja rzędu kilku tysięcy do nawet milionów złotych, w zależności od specyfikacji i producenta. Warto jednak pamiętać, że wybór odpowiedniego urządzenia powinien być oparty nie tylko na jego cenie, ale także na przewidywanych kosztach eksploatacyjnych. Do głównych kosztów operacyjnych należy zaliczyć zużycie energii, która jest kluczowym czynnikiem wpływającym na efektywność ekonomiczną procesu destylacji. Wysokiej jakości destylatory nowej generacji często charakteryzują się niższym zużyciem energii, co może przynieść oszczędności w dłuższym okresie. Dodatkowo, regularna konserwacja i serwisowanie urządzeń również wiążą się z kosztami, które należy uwzględnić w budżecie.
Jakie są najczęstsze problemy związane z użytkowaniem destylatorów przemysłowych
Użytkowanie destylatorów przemysłowych wiąże się z różnymi wyzwaniami i problemami, które mogą wpływać na efektywność procesu oraz jakość uzyskiwanych produktów. Jednym z najczęstszych problemów jest zanieczyszczenie urządzenia, które może prowadzić do obniżenia wydajności oraz jakości destylacji. Zanieczyszczenia mogą pochodzić zarówno z surowców, jak i z samego procesu produkcji. Regularne czyszczenie i konserwacja są kluczowe dla utrzymania optymalnej wydajności destylatora. Innym istotnym problemem są awarie mechaniczne, które mogą wynikać z niewłaściwego użytkowania lub braku odpowiedniej konserwacji. Awarie te mogą prowadzić do przestojów w produkcji oraz dodatkowych kosztów napraw. Ponadto zmiany w składzie surowców mogą wpłynąć na parametry procesu destylacji, co wymaga ciągłego monitorowania i dostosowywania warunków pracy urządzenia.
Jakie są regulacje prawne dotyczące destylatorów przemysłowych
Regulacje prawne dotyczące destylatorów przemysłowych są niezwykle ważne dla zapewnienia bezpieczeństwa oraz ochrony środowiska. W wielu krajach istnieją szczegółowe przepisy dotyczące projektowania, budowy oraz eksploatacji tych urządzeń. Przepisy te obejmują m.in. normy dotyczące emisji substancji szkodliwych do atmosfery oraz wymogi dotyczące zarządzania odpadami powstającymi w procesie produkcji. W przypadku produkcji alkoholu regulacje te są szczególnie rygorystyczne, aby zapobiegać nielegalnej produkcji trunków oraz zapewnić ich jakość i bezpieczeństwo dla konsumentów. Firmy zajmujące się produkcją chemikaliów czy paliw również muszą przestrzegać norm dotyczących bezpieczeństwa pracy oraz ochrony środowiska. Niezastosowanie się do obowiązujących przepisów może prowadzić do poważnych konsekwencji prawnych oraz finansowych dla przedsiębiorstw.
Jakie są perspektywy rozwoju technologii destylacji przemysłowej
Perspektywy rozwoju technologii destylacji przemysłowej są obiecujące, zwłaszcza w kontekście rosnącego zapotrzebowania na efektywne i ekologiczne procesy produkcyjne. W miarę jak przemysł staje się coraz bardziej zrównoważony, technologie związane z destylacją również ewoluują w kierunku większej efektywności energetycznej oraz mniejszego wpływu na środowisko. Innowacyjne rozwiązania takie jak wykorzystanie energii słonecznej czy geotermalnej do podgrzewania cieczy stają się coraz bardziej popularne. Dodatkowo rozwój sztucznej inteligencji i automatyzacji pozwala na optymalizację procesów produkcyjnych poprzez analizę danych w czasie rzeczywistym oraz prognozowanie ewentualnych problemów. Technologie te mogą przyczynić się do zwiększenia wydajności oraz redukcji kosztów operacyjnych w dłuższej perspektywie czasowej.
Jakie innowacje mogą wpłynąć na przyszłość branży destylacyjnej
Innowacje technologiczne mają potencjał znacząco wpłynąć na przyszłość branży destylacyjnej poprzez poprawę efektywności procesów oraz jakości produktów końcowych. Jednym z obszarów intensywnego rozwoju jest zastosowanie nanotechnologii w konstrukcji materiałów używanych w budowie destylatorów. Nanomateriały mogą poprawić właściwości termiczne i chemiczne urządzeń, co przekłada się na lepszą wydajność procesu destylacji. Kolejnym kierunkiem innowacji jest rozwój systemów monitorowania opartych na Internet of Things (IoT), które umożliwiają zbieranie danych o pracy urządzeń w czasie rzeczywistym oraz ich analizę za pomocą algorytmów uczenia maszynowego. Dzięki temu możliwe jest szybsze wykrywanie anomalii oraz optymalizacja warunków pracy urządzeń.
Jakie są kluczowe umiejętności dla pracowników w branży destylacyjnej
Pracownicy w branży destylacyjnej muszą posiadać szereg kluczowych umiejętności, które pozwalają im efektywnie i bezpiecznie obsługiwać skomplikowane urządzenia oraz procesy. Wiedza z zakresu chemii i technologii procesów jest niezbędna do zrozumienia zasad działania destylatorów oraz właściwości przetwarzanych substancji. Umiejętności techniczne, takie jak obsługa maszyn, diagnostyka oraz naprawa urządzeń, są również niezwykle ważne, ponieważ pozwalają na szybką reakcję w przypadku awarii. Dodatkowo, zdolności analityczne i umiejętność pracy z danymi są kluczowe w kontekście monitorowania procesów oraz optymalizacji ich wydajności. Pracownicy powinni także być dobrze zaznajomieni z przepisami prawnymi oraz normami bezpieczeństwa, aby zapewnić zgodność działań z obowiązującymi regulacjami. Wreszcie, umiejętności interpersonalne i zdolność do pracy w zespole są istotne, ponieważ wiele procesów produkcyjnych wymaga współpracy między różnymi działami oraz specjalistami.